Case study - Aeronautics
design exploration: Choosing the best manufacturing method for an aircraft bracket
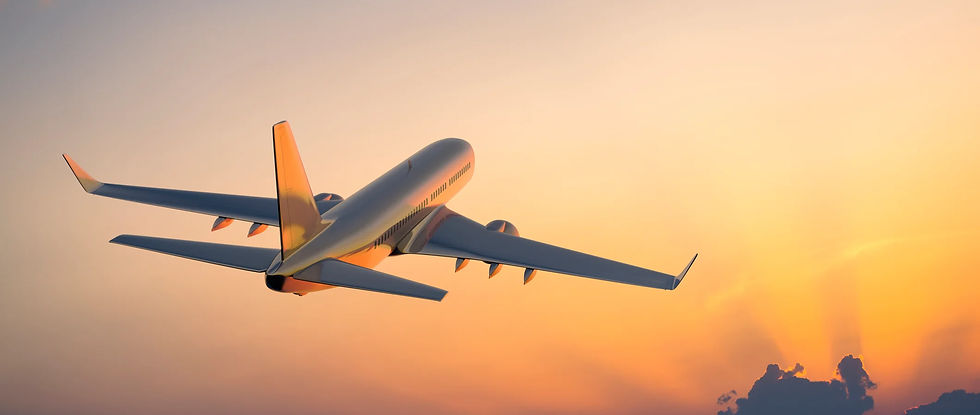
Achieving lightweight structures without compromising performance and business relevance is a key challenge when developing innovative products in aeronautics. Therefore, they must constantly seek the optimal balance between performance (weight and structural integrity), cost, and production scalability to determine the best approach for part development. However, traditional design processes often involve time-consuming iterations between design and manufacturing teams, leading to inefficiencies and delays.
In this case study, Potez Aéronautique leveraged Cognitive Design to accelerate design exploration for an aircraft structural bracket, comparing Additive Manufacturing (AM) and CNC Machining. By embedding Topology Optimization, Simulation-Driven Design (SDD), and Manufacturing-Driven Design (MDD) into a unified workflow, engineers were able to generate, evaluate, and refine multiple design scenarios rapidly. This approach ensured that the final design was lightweight, manufacturable, and cost-effective from the earliest stages.
The outcome
With Cognitive Design, Potez Aéronautique achieved:
-
85% reduction in design exploration time compared to traditional CAD workflows.
-
Faster, informed design decisions based on structural, and cost trade-offs.
-
Seamless manufacturing feasibility validation, minimizing costly iterations and rework.
-
Integrated cost analysis, enabling engineers to make informed-decision from the start.